Adhering to the guidelines associated with design for manufacturing (DFM) ensures that a sheet metal design flows through the processes without issues. This ultimately helps to improve lead times and lowers the overall project cost. Fortunately, there are numerous techniques you can use to increase the chances your sheet metal part is ready for manufacturing.
Before we assess the details of sheet metal fabrication, it’s important to recognize that all sheet metal parts start out flat. Regardless of how complex their final shapes may be, the wall thickness of those parts must be uniform throughout. It’s also important to note that a variety of metals are available, including stainless steel and aluminum, ranging in thicknesses of 0.02 in to 0-.25 in. Beyond sheet metal properties and available materials, here are 5 ways to improve sheet metal parts.
Consider Hole Sizes When Dealing with Sheet Metal
As you’re designing your part and determining where to place holes in your drawing, please keep in mind that you should avoid making holes small enough to break the tool. As the size of the sheet metal hole is reduced, smaller size punches will be required. If the size of the punch becomes too small, it may break during operation. Ideally, the diameter of the hole should be equal or more than the thickness of the sheet metal.
Take an Inside Look at the Inside Radius
As the bend radius gets smaller, the strain in the workpiece increases. When the material’s fatigue point is exceeded, cracks form. Brittle metal, such as aluminum, generally requires a larger bend radius than ductile material like cold-rolled steel.Ductile material works great with small bend radii and short flange depths.
In summary, the 1x Thickness = Inside Radius Rule works for steel, stainless, and other ductile materials. Consult with the fab shop when incorporating a bend radius that is less than the material thickness in the design.
Simplify Your Folds
In general, the more complicated your part is, the more expensive it will be to produce. For this reason, you should design for simple angled bends, with a radius equal to or greater than the thickness of the sheet. Small bends on large, thick parts will often be inaccurate and are both difficult and expensive to produce. When designing your part, you should aim for the simplest design that the part will allow to be the most affordable.
Tooling Considerations
The tooling required to make a part can limit that part’s shape. Conventional press-brake tooling, for example, allows for precision straight-line bends that can be fitted to almost any length and are typically used on most fabricated sheet metal parts. Keeping designs in this shape area allows for lowest cost and fastest manufacturing times. This holds true for features like round embosses, bridge lances, countersinks, extrusions, or other features. These can be typically done in a punch press and every effort should be made to stay with standard sizes when possible.
Precision sheet metal parts and machined parts are different. When designing precision sheet metal parts, note that, because of the multiple processes encompassed in making the parts, these parts are very different from a machined part in terms of what can be manufactured and what tolerances can be held.
Limit the Use of Tight Tolerances
There are typically only a few surfaces of a part that are critical to its function. The more features with tolerance callouts, the more expensive it will be. Some examples of these tolerance callouts include the radii, hole diameters, and distances. For this reason, you should only assign key tolerances to features and surfaces critical to the part’s functionality. When you limit the use of tight tolerances, you will create a more affordable design.
Maintain Uniform Bend Orientation
Maintaining uniform bends throughout your design will increase its affordability. Bends in the same place should be designed in the same direction to avoid part reorientation, which will save both money and time. Keeping a consistent bend radius will make your parts more cost-effective because they will be easier to produce.
CAMM Metals | CT Metal Fabrication Company
It's crucial to do your research when choosing a metal fabrication, as not all companies are capable of completing the same quality of work. CAMM Metals has years of experience, honing our skills across the board to deliver a quality product and measurable bottom line value to our customers.
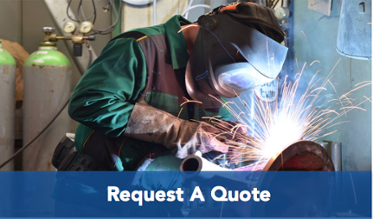